Lead Screws
Lead screws have been around for centuries. These screws are very similar to typical screw and bolt design you may be familiar with from assembling various products. The nut of a lead screw contains a flat surface that rides on the flat surface of the screw flight. The threads of the lead screw can be cut into various different shapes which include trapezoidal (ACME screw), buttress, square threads, and others. These various thread designs offer benefits relative to one another, but all share similar characteristics for efficiency, duty cycle, etc as they compare to a ball screw.
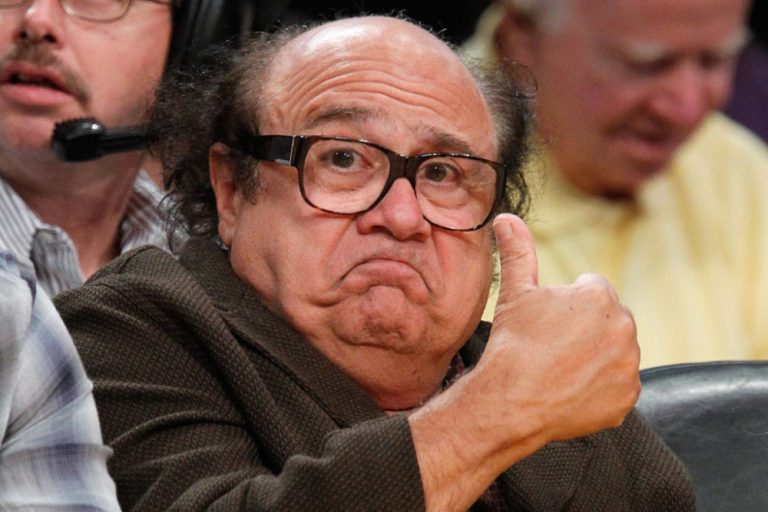
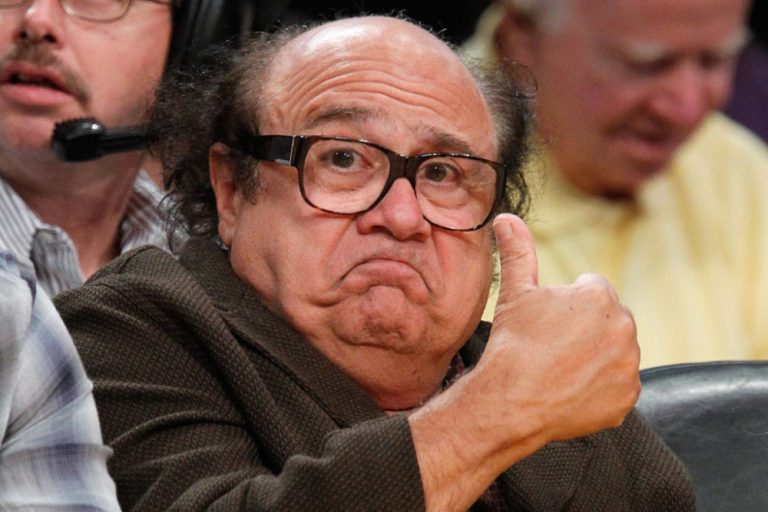
Ball Screws
Ball Screws are named after the recirculating bearing built into the nut design engaging with the screw. These balls rotate and translate along the screw design as they recirculate through the nut, they use a return tube (internal or external) to move back to the front of the pack within the nut and allow the screw to continue moving without any issues.
Ball screws can be very precise or more course in nature. This is typically determined by the screw manufacturing process (is it a ground screw or a rolled screw) and the nut design (is the nut select fit or a general nut that goes with any screw). These different designs result in different ratings for the screw and ultimately different performance levels for noise, critical speeds, load capacities, repeatability, and backlash.
The Results
While some of the differences above are easily noted, the key difference between the two designs is the nut engagement with the screw itself. The ballscrew and the rolling bearing inside result in a much more efficient motion. This efficiency reduces heat in the system, reduces power consumption, and reduces variability in performance over time all the while increasing the load capacity, time before failure, and the duty cycle capabilities.
The lead screw on the other hand utilizing a sliding bearing (friction nut engaged with the screw) has some benefits as well. The friction nut may be able to self-lock (not free fall) or eliminate back driving in situations depending on the screw lead-to-diameter ratio. This means in a vertical situation, the extra expense of the brake may not be needed. The stiction in the leadscew may also help with steady state stability. In a servo system, as the motor dithers (or hunts), the ball screw will translate that motion and decrease your steady state stability – the leadscrew is generally inefficient enough that the servo dither isn’t visible when “in-position”.
Type | Pros | Cons | Typical Applications |
---|---|---|---|
Lead Screws |
|
|
|
Ball Screws |
|
|
|